
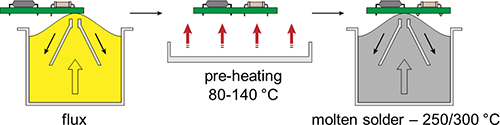
During second stage heating, the differentials increase slightly and again reduced. The temperature-time curves have been measured in a large production furnace in the first step the temperature of the leads of the SOT-23 package rises much faster than that of the leads of the PLCC-68 package and subsequently the temperature-differential are reduced. However this is difficult to obtain in production reflow systems, even if these are fairly long. The ideal situation is where the temperatures of the light and heavy components are practically the same at the end of the homogenizing step, i.e.
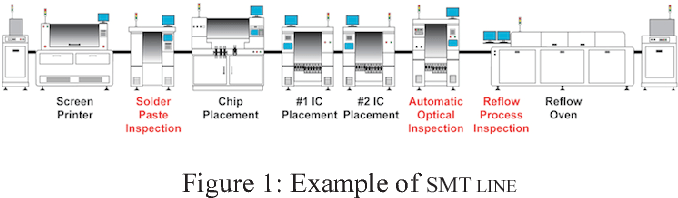
It is furthermore most important that there are no or only small temperature differences between the various components, just before the start of the rapid heating in the soldering phase to avoid any such soldering defects as cold soldering, leaching. Rapid heating in the soldering phase is necessary in order to limit the duration of this phase. There is actually a third method for solder reflow. For the second step the zones in the furnace may be adjusted to produce a kind of temperature plateau in the region between 120 0 C and 1600 C, where the temperature rise is as low as about 0.50K/s and where the temperature differentials can homogenize before the steep rise to the soldering temperature is resumed. Convection reflow provides a more uniform heat distribution to the circuit assembly compared to IR reflow. In practical furnaces, often a three-step heating approach is used: starting with rapid heating, equilibration and again rapid heating. When heating is continued until reflow, some components will have reached an intolerably high temperature. This means that, when a variety of components are soldered simultaneously, some may have already passed soldering temperature, whereas others are still quite far from this temperature. The main difficulty with infra-red soldering of boards with surface mounted components is the different rate of heating of components of different thermal demand. If there are heaters below and above the conveyor (which is usually the case), they mutually influence their temperature control, especially when they can ‘see’ each other. The temperature in an IR furnace, with a mixture of radiation and convection, is ill-defined, and measuring the temperature with a thermo-couple hanging in the furnace has little or no meaning the only useful method is to measure the temperature of a defined product while it is transported through the furnace. The main disadvantage of IR heating is the difference in heating rate, resulting from the different absorption coefficients of the materials used and from the different component thermal masses, related to the surface area that is accessible to IR radiation. Iii) the heating power is easy to control
#Reflow process free#
Ii) the heating is contact free and accurate positioning of the product to be soldered is not necessary I) it is clean and environmental friendly method The heating is chiefly characterized by the wavelength of the elements in the machine.
